In the world of cosplay, armor plays a pivotal role. It not only brings a character to life but also adds a layer of authenticity and intricacy to the costume. A myriad of materials to choose from when making cosplay armor– from foam and thermoplastic to metal and leather. However, one material stands out due to its unique properties – Polyvinyl Chloride, more commonly known as PVC.
PVC pipes, often associated with plumbing or electrical conduits, possess untapped potential in the realm of cosplay armor. Their cost-effectiveness, coupled with their high durability and wide availability, make them an excellent choice for both beginners and seasoned cosplayers alike.
This blog post takes you on a journey, unravelling the process of converting these mundane PVC pipes into awe-inspiring cosplay armor. From the initial design to the final finishing touches, every step unfolds here in detail, arming you with the knowledge to embark on your own cosplay armor crafting journey.
But why PVC, one might wonder? The upcoming sections delve into the advantages of using PVC pipes for cosplay armor, casting light on why they’re worth considering for your next project.
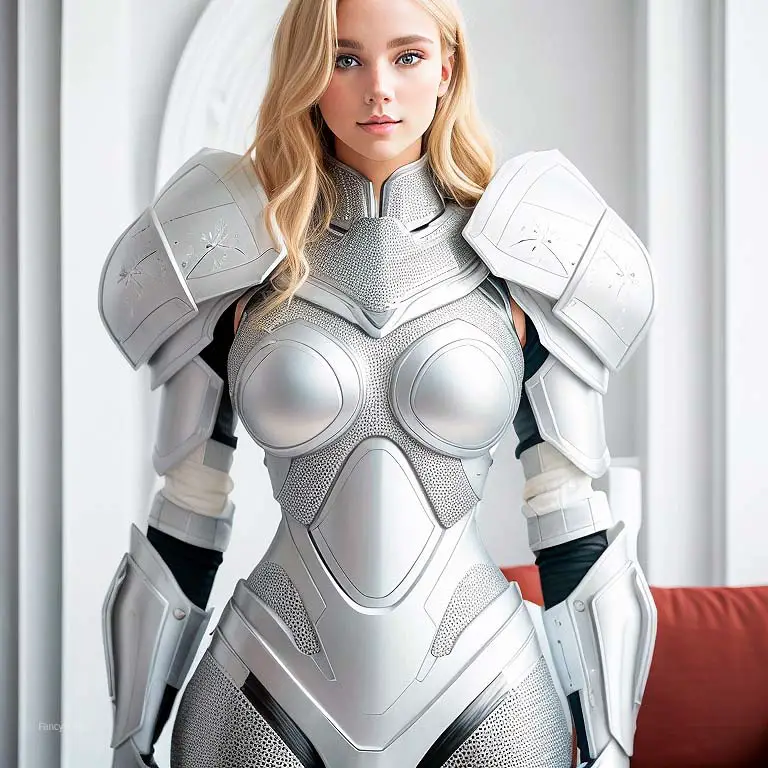
II. Advantages of Using PVC Pipes for Cosplay Armor
Polyvinyl Chloride, better known as PVC, brings numerous benefits to the table when used for cosplay armor. Four core advantages of PVC pipe usage merit further discussion.
Cost-Effectiveness of PVC Pipes
For those on a budget, PVC pipes prove to be an economic choice. They provide great value, considering their durability and the ease of molding them into desired shapes. By spending minimally on the material, you can allocate more resources to other aspects of your cosplay such as accessories or makeup, enhancing your overall look.
Durability and Resilience
PVC pipes boast high strength and resist damage, making them ideal for crafting robust cosplay armor. They withstand pressure, impacts, and even rough handling, ensuring your armor survives the hustle and bustle of conventions. With PVC, you create armor pieces that last, saving you from frequent repair or replacement. Cardboard cosplay armor is also a budget option, but it simply isn’t nearly as durable as PVC pipe built armor.
Easy Availability
PVC pipes enjoy broad availability, found in most hardware stores and online platforms. Their popularity in construction gives them a wide presence, making it easy for you to source them whenever you need. No matter your location, acquiring PVC pipes for your cosplay armor seldom poses a problem.
Flexibility and Ability to Mold
Perhaps the most attractive feature of PVC pipes lies in their versatility. When heated, these pipes become malleable and can take on virtually any shape you desire, fitting perfectly into the world of cosplay where every character comes with unique armor designs. Once cooled, they retain their new form, preserving the hard work you put into shaping them.
PVC pipes offer a combination of cost-effectiveness, durability, availability, and versatility. Together, these features render PVC pipes not just a viable, but an excellent choice for crafting your cosplay armor.
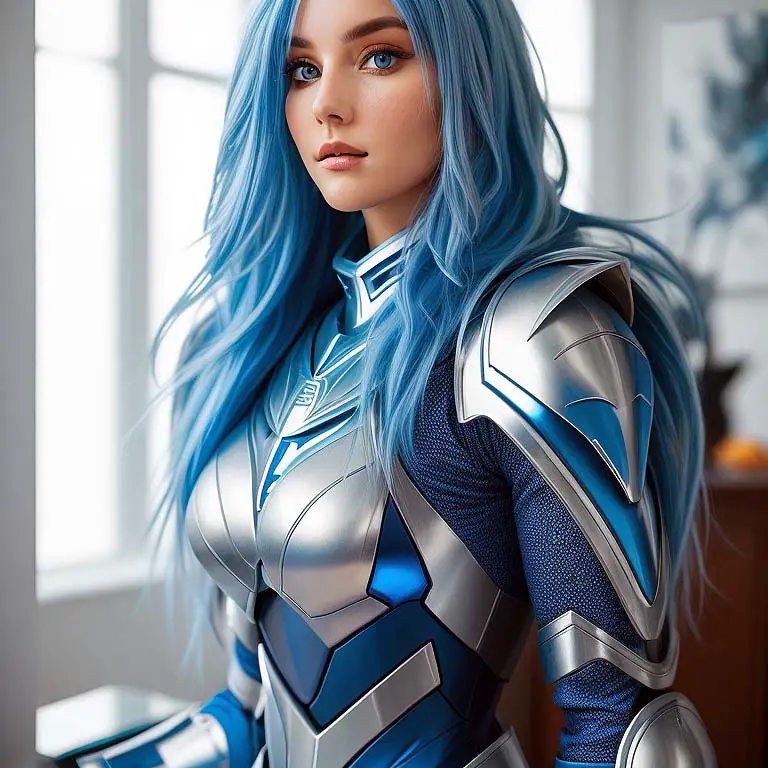
III. Materials Needed for the Project
Before diving into the creation process, it’s crucial to gather all necessary tools and materials. Here’s a detailed list of what you’ll need.
Tools and Materials for Your Project
PVC Pipes: These serve as the primary material for your cosplay armor. The diameter will depend on the particular armor piece you plan on creating. PVC Cutter or Hacksaw: You’ll need this to cut the PVC pipes to the desired size. Heat Gun: This tool allows you to heat the PVC pipes until they become pliable and can be molded into shape. Protective Gloves: To protect your hands from the heated PVC and cutting tools, ensure you have a pair of heavy-duty gloves. Pencil or Marker: For marking cut lines or design outlines on your PVC pipes. Sandpaper: For smoothing rough edges after cutting and shaping the PVC.
Sourcing Your Materials
You can find most of these materials in local hardware stores or online. Consider exploring online retailers for competitive prices and a wider range of options.
Importance of Safety Equipment
Working with PVC and heat can pose some risks. Hence, wearing safety gear like gloves, and even safety goggles and a work apron, becomes crucial. These can protect you from burns when heating the PVC and prevent any accidental injuries when cutting.
Assembling all necessary tools and materials before you begin not only helps keep the process efficient but also ensures safety. With everything in hand, you’re now ready to embark on the exciting journey of transforming PVC pipes into your unique cosplay armor.
IV. Understanding the Basics of Working with PVC
Before manipulating PVC into armor, it’s essential to understand what PVC is and how to handle it safely and effectively.
Brief History and Manufacturing Process of PVC
Polyvinyl Chloride, known as PVC, is a type of plastic recognized for its strength, lightweight nature, and resistance to weathering and chemicals. Since its inception in the early 20th century, PVC has found extensive use in various industries, including construction, healthcare, and, as we now know, cosplay.
PVC’s manufacturing process involves the polymerization of vinyl chloride monomer, resulting in a durable material suitable for various applications. However, its toughness does not compromise its malleability, making it ideal for cosplay armor.
Various Forms of PVC and the Best Types for Cosplay Armor
PVC comes in many forms: pipes, sheets, and even clothing. For our purpose, we focus on PVC pipes, typically used for plumbing and electrical conduits. They offer a perfect blend of rigidity and flexibility, enabling cosplayers to create robust yet intricate armor pieces.
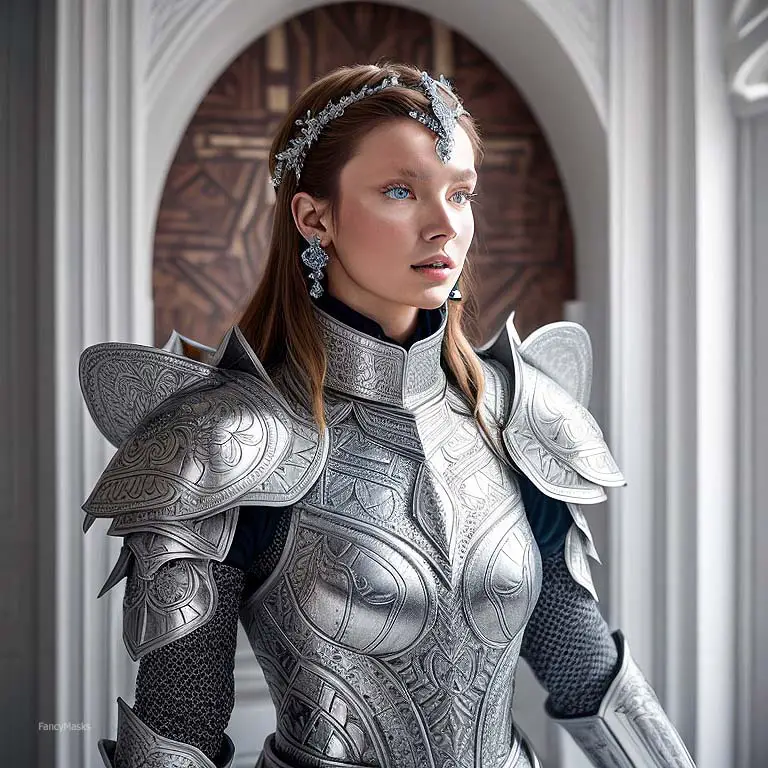
Safety Considerations When Working with PVC
Though PVC proves beneficial in many ways, it requires careful handling. Always work in a well-ventilated area, as heating PVC can release fumes that should not be inhaled.
Ensure you’re equipped with appropriate safety gear, including heat-resistant gloves and safety glasses, to protect from potential burns or flying debris when cutting or shaping PVC.
Understanding the fundamentals of PVC and its safe handling is paramount before you dive into crafting. With this knowledge in hand, you’re well on your way to mastering the art of creating cosplay armor with PVC pipes.
V. Designing Your Cosplay Armor
Creating cosplay armor begins with a clear design in mind. You need to have a defined vision for the final product, which you’ll gradually bring to life.
Researching and Selecting Your Character’s Armor
The first step is to choose the character whose armor you wish to replicate. Spend time studying their armor in detail. Look at images from multiple angles, noting down unique characteristics, colors, patterns, and other design elements. If possible, find blueprints or sketches of the armor online to help guide your design process.
Sketching and Sizing the Armor
After you have a clear picture of the armor, sketch it on paper. This process helps you understand the structure and dimensions of the armor. Ensure your sketch is proportional to your body size. Break down the design into smaller pieces for ease of crafting.
Transferring Your Design to the PVC Pipe
Next, transfer your design from paper to PVC. Use a marker to outline each armor piece on the PVC pipe. Be as precise as possible – the accuracy of your lines will affect the outcome of the final product.
Remember, designing is the foundation of your cosplay armor. Time spent on perfecting your design saves effort in the crafting phase and helps achieve a more accurate, detailed, and impressive end result.
VI. Cutting and Shaping PVC Pipes
Once the design transfer to the PVC pipe is complete, the next step involves cutting and shaping these pipes into your envisioned armor pieces.
Instructions on Cutting PVC Pipes
Using a PVC cutter or a hacksaw, follow the outlines you drew on the pipes. Ensure you cut just outside your lines, allowing for a bit of extra material that you can later refine during the sanding process. Remember to cut carefully to avoid any accidents.
Methods to Heat and Mold PVC Pipes
The key to shaping PVC lies in its thermoplastic nature, which allows it to soften under heat and harden once cooled. Using a heat gun, evenly heat the cut pieces until they become flexible. Then, mold them into the desired shape by hand or over a form that mimics the shape of the part of the body where the armor piece will sit.
During this process, ensure you wear heat-resistant gloves to protect your hands. Additionally, heat the PVC in a well-ventilated area to disperse any fumes.
Safety Tips When Cutting and Shaping PVC
As you engage in cutting and shaping, prioritize safety. Use protective equipment, handle tools with care, and maintain a tidy workspace to minimize risk.
Crafting armor from PVC pipes involves creativity, patience, and meticulousness. Through careful cutting and shaping, you’ll begin to see your sketched designs transform into tangible pieces of cosplay armor.
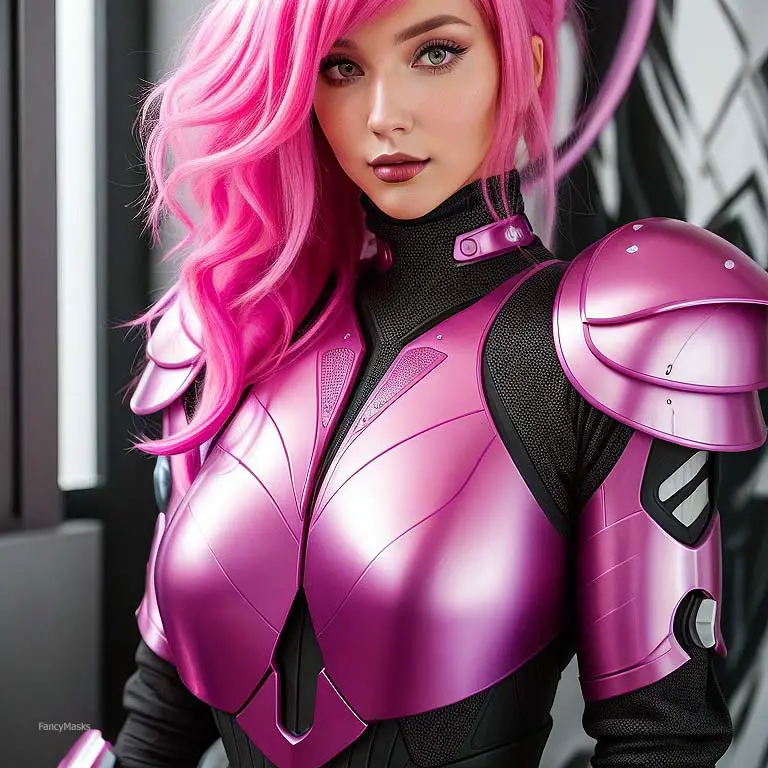
VII. Assembly of Cosplay Armor
With the individual pieces of your armor cut and shaped, you’re now ready to assemble these pieces into a full set of cosplay armor.
Process of Fitting and Adjusting the Pieces
Start by arranging the pieces as per your design. Temporarily attach them using tape or clamps to check the fit and make any necessary adjustments. Remember, comfort is just as important as aesthetics – your armor should not restrict your movement or cause discomfort.
Techniques to Join the Pieces
There are various ways to secure the pieces together, depending on your design and preference.
Glue: PVC cement creates a strong bond between two pieces of PVC. However, it’s irreversible, so be sure of your placement before using it. Rivets: Rivets provide a robust join and also allow for movement between pieces, ideal for areas such as elbow or knee joints. Velcro or Elastic Straps: For pieces that need to be removable or adjustable, consider using Velcro or elastic straps. They provide flexibility and ease of use.
Tips for Ensuring a Comfortable Fit
Always check the fit after joining two pieces. The armor should conform to your body shape and stay in place without being overly tight. Adding padding on the inside of the armor can improve comfort and fit.
Assembling the armor requires patience and precision, but it’s also where your creation starts to take shape. Remember, mistakes are part of the process. If a piece doesn’t fit right, take it apart and try again. With each step, you’re getting closer to your fully realized cosplay armor.
VIII. Painting and Finishing Your Cosplay Armor
The final stage in creating your PVC pipe cosplay armor is adding colors and finishing touches that bring your design to life.
Preparing the PVC Surface for Painting
PVC requires a bit of preparation to ensure the paint adheres properly. Start by using fine-grit sandpaper to roughen the surface slightly. Then, wipe down the armor with a damp cloth to remove any dust or debris.
Selection of Paints and Techniques
When it comes to painting PVC, not all paints are equal. Acrylic paints are a common choice due to their wide color range and ease of use. For a smoother finish and longer-lasting color, consider using a primer before the actual color coat. Remember to finish with a clear sealer to protect the paint from chips and scratches.
Adding Details and Accents
Once the base coat of paint has dried, it’s time to add the details. Use smaller brushes to add intricate patterns or shading that mirror your chosen character’s armor. Metallic paints can simulate the look of metal, while gloss or matte top coats can adjust the overall sheen of your armor.
Final Touches and Quality Check
After all paint has dried and you’re satisfied with the look, do a final quality check. Ensure all pieces connect correctly, the paint job is smooth, and the armor fits comfortably.
Painting and finishing your cosplay armor is a meticulous process that requires a steady hand and a keen eye for detail. But it’s also one of the most rewarding stages, as it’s when your armor truly comes to life and transforms into a part of your chosen character.
X. Conclusion: The Rewards of Creating Your Own Cosplay Armor
Crafting your own cosplay armor from PVC pipes might seem daunting at first, but the rewards outweigh the challenges. Not only does it allow you to tailor your costume to your exact specifications, but it also fosters a sense of accomplishment and connection with the character you portray.
When you step into a convention wearing armor you created, you’re not just displaying a costume. You’re showcasing hours of dedication, skill, and creativity. Each piece tells a story of your crafting journey, from the first design sketch to the final layer of paint.
So, whether you’re a seasoned cosplayer or a novice, consider the art of crafting your own cosplay armor. It’s a rewarding journey into the heart of your favorite characters, made all the more special by your personal touch. We love seeing images of what our users create so feel free to share your creations with us on our instagram page.