As a cosplayer, you know that the details are what make your costume stand out. And when it comes to creating armor, foam is a versatile material that can help you achieve those details without breaking the bank. Foam has become increasingly popular in cosplay communities around the world because of its affordability and ease of use.
It’s a lightweight material that can be shaped, cut, and molded into just about any form imaginable. Plus, it’s readily available at most craft stores or online retailers. Foam casting is also far less expensive than thermoplastic or resin casting.
The best part? You don’t need to be an expert prop maker or have access to fancy tools to start working with foam.
All you need is some creativity, patience, and basic supplies like a utility knife and heat gun. One of the biggest benefits of using foam for cosplay is how forgiving it can be.
Unlike other materials like metal or resin, foam won’t bruise or break if you accidentally drop it on the floor (trust me on this one). Plus, foam is much more lightweight than other traditional materials used in prop-making such as wood or metal.
Another great benefit of working with foam for cosplay is its versatility when it comes to creating complex shapes and designs. With some simple techniques like heat shaping or carving with a utility knife, you can create intricate details that would be difficult to achieve with other materials.
Overall, working with foam offers an accessible way for cosplayers at all skill levels to create impressive armor and props without resorting to expensive materials or equipment. In this guide we’ll cover everything from basic techniques like cutting and gluing pieces together to more advanced methods like carving intricate designs into foam pieces – so let’s get started! If this feels a little more advanced, our full guide to cosplay crafting can help you pick an approach for any skill level.
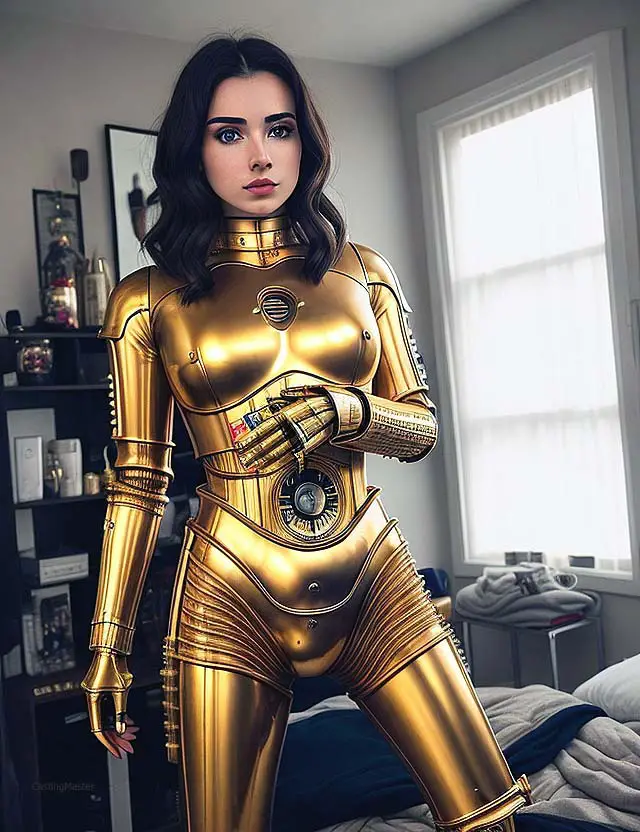
Types of Foam
Foam is a versatile material that can be used in a variety of ways for cosplay crafting. Two of the most commonly used types of foam for cosplay are EVA foam and craft foam. Both EVA and craft foam have their pros and cons, which we’ll discuss below to help you decide which is best for your needs.
EVA Foam
EVA stands for Ethylene-vinyl acetate, and it’s a type of foam commonly used in athletic equipment and footwear. It’s also popular among cosplayers because it’s durable, lightweight, and easy to work with. EVA foam comes in various thicknesses, textures, and colors, making it an ideal choice for both armor and props.
One advantage of EVA foam is that it can be heat-formed using a heat gun or a hairdryer. This means you can create complex shapes by heating up the foam until it becomes pliable enough to mold into the shape you want.
Once cooled down, the shape will hold its form. However, one downside to this type of foam is that it tends to retain some memory from the way it was originally molded.
Another advantage of EVA foam is that it can easily be sanded or carved to add details or create texture on props or armor pieces. Additionally, EVA foam has good shock absorption qualities which make it perfect for creating weapons like swords or hammers.
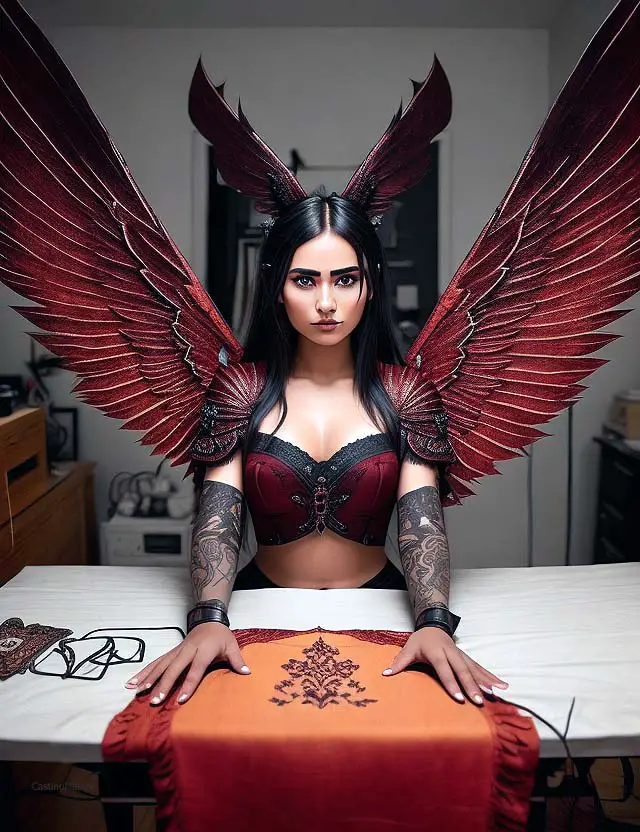
Craft Foam
Craft foam is another popular choice amongst cosplayers due to its affordability and accessibility – you can find this type of foam in most craft stores around the world! Craft foams come in different sizes (thickness), colors & patterns; making them a great option when looking for different things like wings or headpieces. The main drawback with craft foams is its durability – they are not as strong as other types of foams, which means that they will bend or deform under stress.
This makes craft foam less ideal for creating armor or weapons. However, one advantage of using craft foam is its flexibility.
It can be easily cut with scissors and glued together with hot glue to create a variety of shapes and designs for accessories such as headbands or bows. Additionally, because this type of foam is lightweight, it’s comfortable to wear for extended periods.
When it comes to deciding between EVA foam and craft foam, it all boils down to the intended use of your cosplay piece. EVA foam is ideal for creating armor that requires durability and structure while craft foam is suitable for smaller items like headpieces and accessories that require flexibility.
Choosing the right type of foam can make a significant difference in the final outcome of your cosplay project. Take into consideration your cosplay goals and choose the right material that best suits your needs!
Tools and Materials
The Must-Haves
When it comes to working with foam, there are a few tools that are absolutely essential for success. First and foremost, you’ll need a utility knife. This will be your go-to tool for cutting foam to shape, so make sure you have a sharp blade and plenty of replacements on hand.
Additionally, a heat gun is another must-have tool for working with foam. It can be used to help shape and mold the foam by softening it up, making it easier to work with.
Additional Tools
While a utility knife and heat gun are the most important tools for working with foam, there are some additional tools that can make your life easier. For example, scissors can be used to cut thin pieces of foam or fabric.
A rotary cutter is another option that may work well if you’re cutting lots of straight lines in foam or fabric. Another useful tool for working with foam is an electric carving knife.
This can be especially helpful if you’re working on larger pieces of foam or need to make intricate cuts. Other useful items include sandpaper, files or rasps (for smoothing edges), clamps (for holding pieces together while glue dries), and rulers (for measuring).
Adhesives
Foam is not exactly easy to glue together using traditional adhesives like school glue or hot glue – these just don’t stick effectively enough! Instead, many people swear by contact cement as the best adhesive option for foam crafting. Contact cement is applied in two stages – first on one surface and then on the other – before being allowed to dry completely before joining the two surfaces together.
Another popular adhesive option among cosplayers is Plasti-Dip sprayable rubber coating that creates a smooth finish over projects made from EVA Foam which also makes them more durable. It can be used for sealing foam edges, creating a smooth surface for painting, and even to create texture.
Safety Gear
When working with foam it’s important to keep safety in mind. Make sure to wear gloves to protect your hands from the heat of the heat gun and sharpness of the knife.
Additionally, a mask or respirator should be worn when sanding or cutting foam since it can produce small particles that can irritate your lungs. Eye protection is also recommended when using a heat gun.
Where to Find Supplies
Now that you have an idea of what tools and materials you’ll need for working with foam, where do you find them? Many craft stores carry EVA foam and other essential supplies along with online stores like Amazon or specialized cosplay supply retailers which also carry unique tools tailored specifically for cosplayers. Don’t forget to shop around since prices may vary depending on where you buy them!
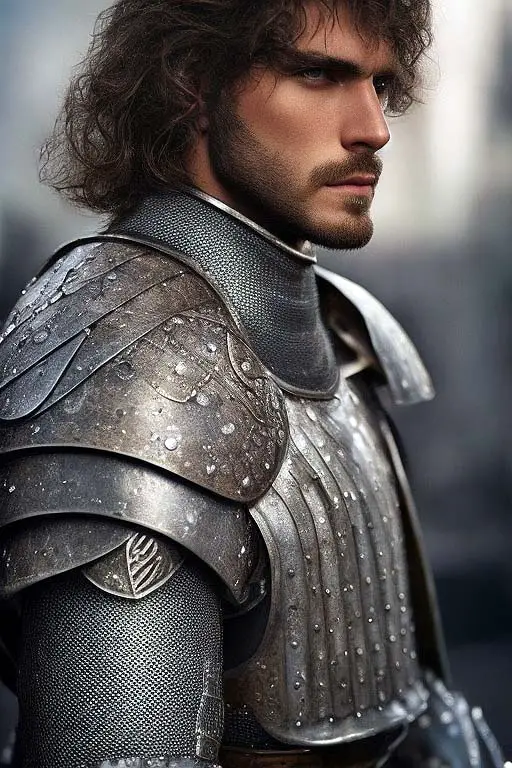
Basic Techniques
Cutting Foam
When cutting foam, it is important to use a sharp utility knife or blade. This will help create clean cuts and prevent the foam from tearing or fraying.
Before cutting, mark out your desired shape on the foam using a pen or marker. For straight cuts, you can use a ruler as a guide to keep your lines straight.
For curved cuts, it can be helpful to cut small sections at a time and gradually work your way around the curve. This will help prevent mistakes and ensure that you get smooth, even curves.
Shaping Foam
Once you have cut out your basic shapes, you can start shaping them further using heat. A heat gun can be used to soften the foam and make it more pliable. Once heated, you can bend and shape the foam into more complex curves or details.
Be careful when using heat on foam as it can melt or burn if left in one place for too long. Always keep the heat gun moving and test on scrap pieces before working on your final project.
Gluing Foam Pieces Together
To assemble different pieces of foam together for armor or props, contact cement is often used. Apply a thin layer of contact cement to both pieces of foam that will be joined together and allow them to dry for several minutes until they are tacky.
Then press the two pieces together firmly and hold them in place for several minutes until they adhere securely. If needed, additional layers of contact cement may be added for increased strength.
Tips for Clean Cuts
One tip for getting cleaner cuts with less fraying is to use a brand new blade every time you start cutting new foam sheets. It’s also helpful to apply light pressure while cutting so that the blade glides smoothly through the material without snagging it. Another tip is to cut in a fluid, sweeping motion instead of stopping and starting again.
Stopping and starting can cause jagged edges or even small undercuts that might mar the foam. Plus, a smooth, continuous cut will result in less clean-up work later on.
Tips for Smooth Edges
To get smoother edges on your foam pieces, you can use a sandpaper block or a Dremel tool with a sanding attachment. This will help remove any rough spots or bumps and give your foam pieces a more polished look.
It’s important to sand gently and use light pressure so that you don’t deform the shape of your foam piece. A gentle hand is especially important if you’re working with thinner sheets of foam that could be easily dented or damaged by rough handling.
Advanced Techniques
Carving Designs into Foam
When it comes to creating intricate designs on foam, carving is the way to go. This technique allows you to add depth and dimension to your foam armor or props.
To get started, you’ll need a sharp knife or carving tool. Exacto knives are great for smaller details while larger blades like box cutters can make quick work of larger areas.
Before carving, it’s important to have a clear idea of what you want your design to look like. Sketch out your design on paper and then transfer it onto the foam with a pencil.
Starting with a rough outline of your design, slowly carve away at the foam until you’ve achieved the desired shape. To add even more detail, try layering multiple pieces of foam together and carving them as one piece.
This technique works well for adding depth and creating three-dimensional designs. Some popular examples of carved foam designs in cosplay include intricate dragonscales on armor or detailed runes etched into mage staffs.
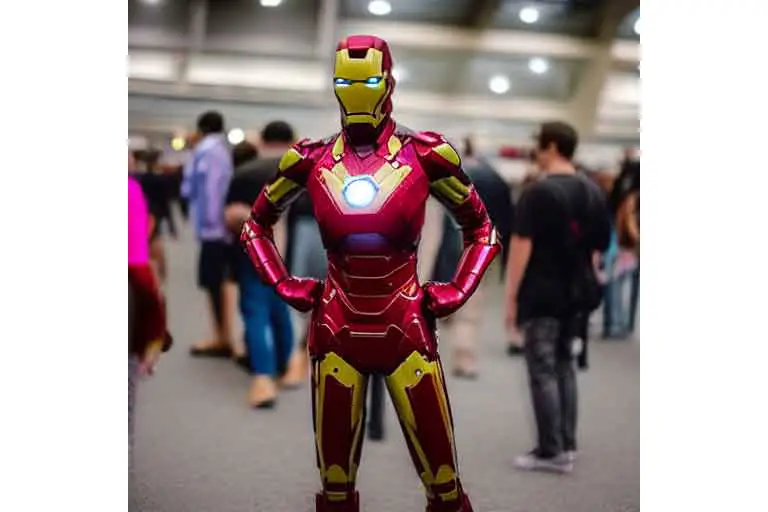
Creating Texture with Heat
Another advanced technique for working with foam is using heat to create texture. By heating up the surface of the foam, you can create interesting patterns that mimic textures found in nature or on man-made objects.
To get started, heat up your heat gun and hold it close (but not touching) the surface of your foam piece. Move the gun around in circular motions until you start to see the surface melt slightly.
Keep moving around until you’ve created an interesting texture. Some popular textures created with this technique include cracked stone surfaces or rough tree bark patterns on mage staffs.
Examples from Popular Cosplay Builds
One example of advanced foam crafting can be seen in Kamui Cosplay’s World of Warcraft Night Elf Demon Hunter cosplay build. The armor set includes intricate carved designs combined with realistic-looking texture created using heat.
The finished product creates a stunningly realistic look that seems to have come straight out of the game. Another example comes from Volpin Props’ BioShock Big Daddy build.
The intricate design of the helmet and armor pieces were all carved out of foam and then coated with various paints and finishes to create a convincing metal look. These advanced techniques take time and practice to perfect, but with dedication and patience, you can create impressive-looking foam armor or props for your next cosplay build.
Painting Foam
Avoiding Common Painting Mistakes
Once you’ve crafted your foam armor or props, it’s time to paint them to give them a finished look. But painting foam can be tricky if you don’t know what you’re doing. Here are some common mistakes to avoid when painting foam:
– Not using a primer: Foam is porous, which means that the paint can seep into the material and leave a blotchy finish. To avoid this, always use a primer before painting your foam pieces.
– Using the wrong type of paint: Not all paints are created equal, and some types of paint won’t adhere properly to foam. Acrylic paints are usually the best option for painting foam, as they dry quickly and create a smooth finish.
– Applying too much paint: When painting foam, it’s important not to apply too much paint at once. This can cause the foam to become saturated and lose its shape.
Instead, apply thin layers of paint and allow each layer to dry before applying another. Now that you know what not to do when painting foam, let’s talk about some tried-and-true methods for achieving a professional-looking finish.
Spray Painting
Spray painting is one of the easiest ways to give your foam pieces a uniform coat of color. Here’s how to do it:
1. Choose an outdoor or well-ventilated area. 2. Lay out your pieces on newspaper or cardboard.
3. Shake your spray can thoroughly before use. 4. Hold the can about 6 inches away from your piece and spray in sweeping motions.
5. Allow each layer of paint to dry before adding another. One thing to keep in mind with spray painting is that it can be difficult to achieve fine details or intricate designs using this method.
Brush-On Techniques
If you want more control over your paint job, brush-on techniques might be the way to go. Here are some tips for brush-on painting: 1. Choose a soft-bristled brush.
2. Thin your acrylic paint with water to create a smooth consistency. 3. Apply thin layers of paint using light, even strokes.
4. Allow each layer of paint to dry completely before adding another. Using brushes gives you more control and precision when adding details or designs to your foam pieces.
Adding Texture
If you’re looking to add texture to your foam pieces, there are a few methods you can try: – Drybrushing: Dip a dry brush into paint and then wipe most of it off so only a small amount remains on the bristles. Then lightly drag the brush across the surface of your foam piece in short strokes, creating subtle highlights and shadows.
– Weathering: Use a sponge or rag to dab on darker colors over your base coat, then use sandpaper or steel wool to distress the surface and reveal the base color underneath. With these tips in mind, you’re ready to take your foam crafting skills to the next level by painting and adding texture for an even more realistic finish!
Troubleshooting Common Issues
Warping Foam
One issue that many foam crafters encounter is warping. This happens when the foam is heated or stretched unevenly, causing it to bend or curve in unintended ways.
To prevent this from happening, always try to heat your foam evenly across the surface. If you’re using a heat gun, move it in smooth and even strokes rather than focusing on one spot for too long.
Additionally, try not to stretch your foam too much as this can cause it to warp. If your foam has already warped, there are a few things you can do to fix it.
You can try reheating the affected area and reshaping it into its desired shape. Alternatively, you can use a heat gun or hairdryer to apply heat while gently bending the foam in the opposite direction of the warp until it straightens out.
Uneven Seams
Another common issue with foam crafting is creating uneven seams where two pieces of foam are glued together. This occurs when there is too much glue between the layers or if one layer is thicker than the other. To avoid this problem, make sure that you apply an even amount of glue on both surfaces before pressing them together.
If your seams are already uneven, don’t worry – there’s still hope! Use a sanding block or rotary tool with a sanding attachment to smooth out any bumps or lumps along your seam lines until they blend seamlessly into each other.
Conclusion
Working with foam for cosplay can seem intimidating at first but with some practice and patience, anyone can create amazing props and armor pieces! Remember to start small and work your way up as you gain more experience – nobody becomes an expert overnight!
Don’t be afraid to experiment with different techniques and materials – sometimes the most unexpected methods yield amazing results. And always remember to have fun!
At the end of the day, cosplay is all about expressing your creativity and having a good time. Happy crafting!