If you’re someone who loves cosplay, chances are you’ve heard of resin casting. It’s a popular technique used to create highly detailed and accurate props, armor pieces, and accessories for your cosplay costumes.
But what exactly is resin casting, and why should you consider using it in your cosplay projects? At its most basic level, resin casting involves pouring liquid resin into a mold and waiting for it to harden into a solid shape. This is one of the more advanced options, so if you’re more of a beginner we have a general guide to cosplay armor.
But while the process may seem simple on the surface, there are many different factors that can impact the end result of your cosplay resin casting. Choosing the right materials, mixing them correctly, and creating a good mold are all important steps that can make or break your final product.
So why bother with resin casting at all? There are several benefits that make it an appealing choice for many cosplayers:
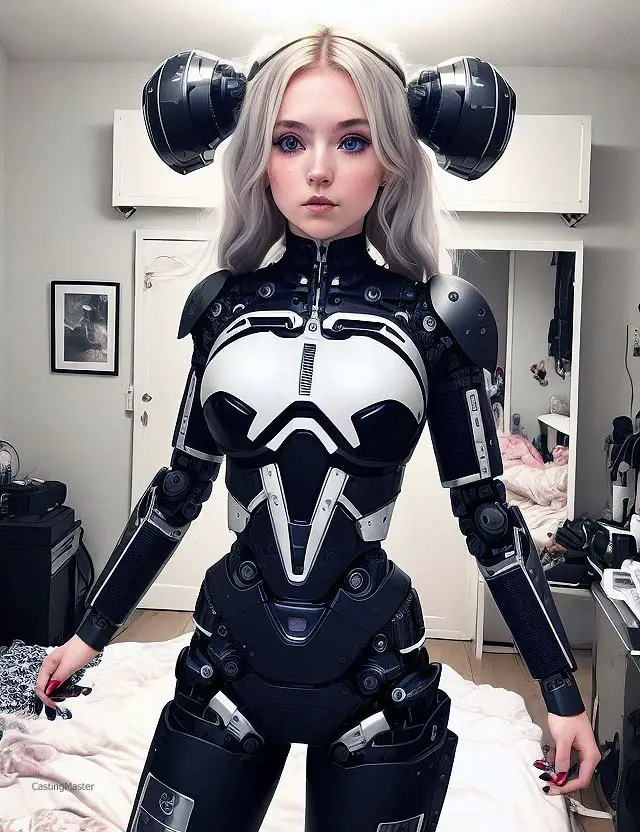
High level of detail
Resin is an excellent material for capturing intricate details in your molds. Whether you’re creating armor pieces with complex designs or reproducing weapon props with lots of intricate lines and textures, resin can help ensure that every detail is preserved in the final product.
Durability
Once cured, resins tend to be very strong and durable materials. This makes them ideal for creating props and armor pieces that need to stand up to wear-and-tear over time.
Versatility
Resin comes in many different varieties with varying properties depending on your specific needs. You can choose from clear or opaque resins in different colors or finishes (such as matte or glossy). Additionally, some resins are more flexible than others which may be beneficial depending on what you’re making.
Cost-effective
While there may be some initial investment required to purchase the necessary tools and materials (such as silicone molds), overall resin casting can be a cost-effective way to create highly detailed props and armor pieces that might otherwise be difficult or expensive to obtain. If you’re looking for something that’s less expensive that resin casting, we’ve created a full guide to cosplay crafting here.
Customization
When you make your own molds and castings, you have complete control over the final product. You can tweak the design and details as much as you want until it’s perfect for your cosplay needs. This is especially important for cosplayers who create original designs or characters that don’t have existing merchandise available.
In the end, resin casting is a technique that offers a lot of benefits for cosplayers who are looking to take their costuming skills to the next level. With a little bit of practice and experimentation, you can create amazing props and armor pieces that will help bring your cosplay vision to life.
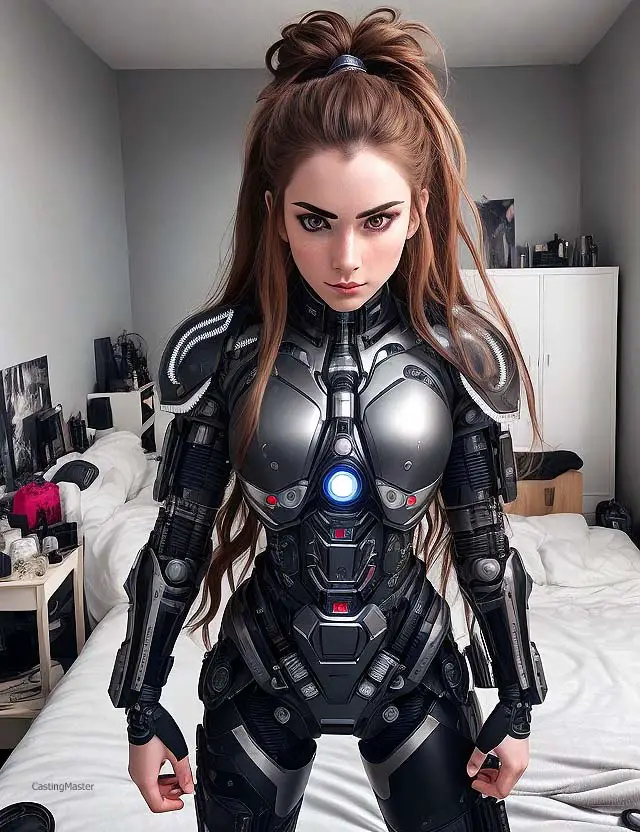
Materials Needed
Resin casting for cosplay requires a variety of materials to get started. Here are the essentials:
Resin
The first and most important material you will need is the resin itself. Resin comes in different types, such as epoxy or polyester, and each has its own strengths and weaknesses.
Epoxy resin is generally considered stronger and more durable, while polyester resin is less expensive. However, polyester resin may not be suitable for all projects due to its strong odor.
When choosing a resin type, consider your project’s requirements and your level of experience with resin casting. You should also keep in mind that certain resins have different pot lives (the time it takes for the mixture to start hardening) and cure times (the time it takes for the mixture to fully harden) which can affect your ability to work with them.
Mold
To cast a piece in resin, you’ll need a mold into which you’ll pour the liquid material. Molds can be made of various materials like silicone or plaster.
Silicone molds are popular among cosplayers because they can capture fine details and easily release their contents after curing. Silicone rubber molds come in two varieties; tin-cured (condensation-cured) or platinum-cured (addition-cured).
Tin-cured silicones are cheaper but may take longer to cure than platinum-cured ones. When making your own mold, make sure that it’s appropriate for your project size and that it includes all necessary details like undercuts or texturing.
Release Agent
A release agent is used on molds so that the hardened resin doesn’t stick when demolding. A variety of release agents exist such as petroleum jelly or cooking spray but also specific products designed solely for this purpose.
Before pouring in your resin mixture, use a brush to apply the release agent to the inside of your mold. Don’t forget that for larger molds, you may need to apply multiple coats.
Mixing cups
When mixing your resin, it’s important to use accurate measurements so that the mixture sets properly. Mixing cups are essential for this purpose as they typically have marked measurements on their sides.
You’ll need at least two cups: one for measuring and another for mixing. Be sure to use disposable cups or one specifically designated for resin casting as leftover residue can contaminate future mixtures.
Stirring tools
Mixing resin requires precise measurements and equally precise mixing of all elements involved. To ensure an even mixture, a stir stick is needed.
You can use disposable plastic spoons or popsicle sticks or a specific tool like a silicone spatula. Avoid using wooden stir sticks as resin may absorb into the wood causing deformed castings in future projects.
Choosing Your Materials
When selecting materials, always choose based on your project requirements and experience level with resin casting. Additionally, consider the materials’ pot life, cure time and quantity needed when choosing them. With these essential materials in hand, you’ll be able to start creating amazing pieces using the resin casting technique for cosplay!
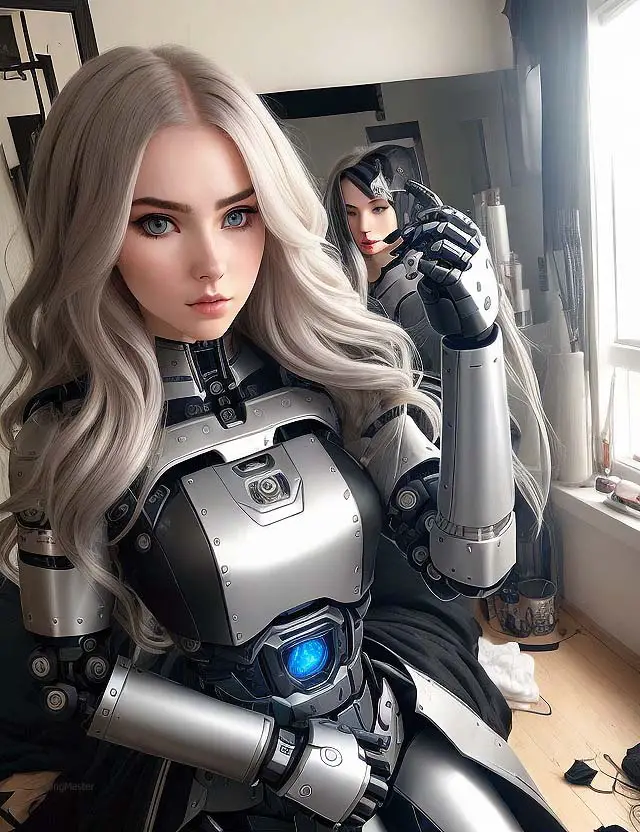
Making a Mold
Silicone vs. Other MaterialsWhen it comes to making molds, silicone is the most commonly used material in resin casting for cosplay. It’s easy to work with, reusable, and produces high-quality molds. However, there are other materials you can use to make molds as well, such as latex or alginate. Silicone has some distinct advantages over these other materials. For example, it’s more durable and can be used with a wider variety of resins without breaking down or reacting poorly. That being said, some people prefer using alternative mold-making materials because they’re more affordable or have different properties that work better for specific applications.
One-Piece vs. Two-Piece MoldsMolds come in different types and configurations depending on what you’re casting and how complex your object is. One-piece molds are the simplest type of mold to make and use – you simply pour the silicone over your object and let it cure into a solid block that can be removed from the object once it’s dry. Two-piece molds are a bit more involved but allow for greater detail in your casts. With this type of mold, you create two separate pieces that fit together snugly around your object before pouring in the resin. Two-piece molds are generally preferred when creating complex or detailed objects because they allow for greater precision in capturing all the details of your original piece.
Pros and Cons of Each Type
There are pros and cons to both one-piece and two-piece molds that should be considered before deciding which type to make for your project. One-piece molds are easy to make since you don’t have to worry about aligning multiple pieces together during casting – this is especially useful if you’re new to resin casting or working with simpler objects.
However, they may not capture as much detail as two-piece molds since the mold has to be removed from the object in one piece and may distort slightly during this process. Two-piece molds require more work during the mold-making stage, but they produce more accurate results since you can avoid distortion from removing a single piece mold.
They are also useful for objects that have undercuts or complex details that require multiple pieces to be cast separately before assembly. Unfortunately, they are typically more difficult to create accurately and can be trickier to align properly during casting due to the multiple pieces involved.
Mixing Resin
The Importance of Proper Mixing in Resin Casting
Mixing the right amount of resin and hardener is crucial to the success of your resin casting project. The ratio of resin to hardener can vary depending on the brand and type of resin you use, so be sure to read the instructions carefully before beginning.
Tools You Will Need to Mix Resin
You will need a few key tools in order to mix your resin properly. The first is a mixing cup, which should be made from a material that won’t react with the chemicals in your resin or hardener. I recommend using plastic cups that are specifically designed for mixing resins.
You will also need something to stir your mixture with, such as a wooden or plastic stir stick. Avoid using metal utensils, as they can cause a reaction with the chemicals in your mixture.
It’s important to wear gloves while working with resin and hardener. The chemicals can irritate your skin or cause an allergic reaction, so protect yourself by wearing nitrile gloves.
How to Mix Resin Properly
Once you have all of your tools gathered and you’re wearing gloves, it’s time to start mixing! Begin by pouring the recommended amount of resin into your mixing cup, being careful not to spill any outside the cup. Then add an equal amount (or whatever ratio is recommended) of hardener into the same cup.
Use your stirring tool and begin stirring slowly but thoroughly until both components are fully mixed together. Be sure that there are no streaks or unmixed spots in the mixture – these could cause problems when casting.
It’s important not to overmix or undermix your resin – this could lead to improper curing times or other issues when casting. Follow any manufacturer guidelines for how long you should stir for and how long the mixture needs to rest before casting.
Safety Precautions When Working with Resin and Hardener
Resin and hardener can be dangerous chemicals if not handled properly. It’s important to always wear gloves when mixing, pouring, or handling your resin.
Additionally, it’s a good idea to work in a well-ventilated area to avoid inhaling fumes. If you accidentally spill any resin or hardener on your skin, immediately wash it off with soap and water.
If you get any in your eyes or mouth, seek medical attention right away. It’s also a good idea to have a first aid kit nearby in case of accidents.
Make sure that you store your resin and hardener properly when not in use. Keep them out of direct sunlight and at the correct temperature (as directed by the manufacturer) to ensure they don’t go bad or expire before you’re ready to use them again.
Mixing resin is an important step in any resin casting project. By following these tips for proper mixing techniques and safety precautions, you can help ensure that your project turns out exactly as planned. Remember – safety first!
Casting Resin
Pouring Resin into a Mold
Now that you’ve made your mold, it’s time to start casting! Here’s a step-by-step guide on how to pour resin into your mold.
First, prepare your work area. Place your mold on a flat surface and cover it with a release agent.
This will help the resin release from the mold once it has cured. Next, measure out the correct amount of resin and hardener according to the manufacturer’s instructions.
Be sure to use a mixing cup specifically designed for resin casting as other cups may react with the chemicals. After measuring out both components, mix them together thoroughly using a stir stick.
It’s important to mix well in order to activate the curing process properly. Now you’re ready to pour!
Slowly pour the resin into your mold, making sure to fill all of the cavities evenly. You want to avoid overfilling or underfilling any part of the mold as this will cause issues with curing and can ruin your piece.
Avoiding Air Bubbles and Ensuring an Even Pour
One of the biggest challenges when casting resin is avoiding air bubbles. Air bubbles can cause unsightly imperfections in your finished piece so it’s important to take steps to prevent them from forming during casting. The first step is thoroughly mixing your resin before pouring.
Mixing creates heat which causes air bubbles so make sure everything is properly mixed before starting. It also helps if you pour slowly and at an angle.
A slow pour allows any air bubbles that do form time to pop on their own while tilting the mold slightly can help remove any trapped air from hard-to-reach areas within your mold. Another technique is using a heat gun or torch lightly over top of poured liquid which heats up material causing any air pockets still in liquid rise up and escape through the surface.
It’s important to not hold it too close as it may damage your mold or even worse, cause fire if you’re using flammable resin. Tapping the sides of the mold gently with a toothpick or something similar can help release any air bubbles that may be trapped inside.
Tap all over the mold including spots that are hard to reach. By following these techniques and tips, you can achieve a smooth, bubble-free finish on your resin cast piece.
Demolding and Finishing
Removing Your Finished Piece from the Mold
Once your resin has cured, it’s time to remove your piece from the mold. Begin by gently pulling on the edges of the mold to loosen it.
If you’re having trouble, try placing the mold in warm water for a few minutes to soften it up. Use a craft knife or scissors to carefully cut away any excess mold material that may be holding your piece in place.
Be cautious not to cut into your resin piece when removing it from the mold. If you’re working with a two-piece mold, carefully separate each half of the silicone or rubber and gently remove the casted piece.
Sanding
Once you have removed your resin piece from its mold, you may find that there are rough edges or imperfections that need to be smoothed out. Sandpaper is an excellent tool for this job!
Start with a coarse grit sandpaper (around 80-120 grit) and work your way up gradually to a finer grit (400-600 grit). When sanding, use long strokes and apply even pressure across the surface of your piece.
Be careful not to press too hard in one spot or you will create an uneven surface. If you’re working on a small area that needs extra attention, consider using a Dremel tool with sanding attachments for precision work.
Painting
Painting is another great way to add detail and personality to your finished resin pieces! Before painting, make sure that any sanding dust has been thoroughly removed from your piece.
To begin painting, apply primer first as this will help paint adhere better and prevent chipping or peeling later on. Allow primer coat(s) to dry completely before moving onto color coats.
When applying color coats, use thin layers rather than one thick layer as this will ensure a more even coverage. Once your final coat is dry, use a clear coat to seal the paint and give it a glossy finish.
Adding Additional Details
If you’re not quite satisfied with your finished piece, consider adding additional details to take it to the next level! Depending on your piece, this could include attaching jewels or other embellishments, using hot glue to add texture, or using epoxy putty to sculpt new elements onto your piece. You can also really age this type of the armor and props.
When adding additional details, don’t be afraid to experiment and have fun! This is where you can really make your piece unique and showcase your creativity.
Clean-Up
Once you have finished working on your resin casted pieces, make sure that all materials are cleaned up properly. Any leftover resin or mold material should be disposed of according to manufacturer instructions or local regulations.
Be sure that all mixing cups and tools are thoroughly cleaned with soap and water before reusing them for future projects. Remember that safety is key when working with any chemicals!
Demolding and finishing are important steps in the resin casting process that can really bring your cosplay pieces to life. By using sanding techniques, painting methods, and adding extra details as desired; you can truly create one-of-a-kind cosplay props that are unique expressions of yourself. Be creative and don’t be afraid to try new techniques – happy casting!
Troubleshooting Common Issues
Sticky Molds: Avoiding the Pitfalls of Improper Release Agents
One of the most common issues that arise during resin casting is sticky molds. This can happen due to improper application or use of release agents. Release agents are an essential tool in preventing resin from sticking to your mold.
Without proper release agents, your mold may become damaged or unusable. One way to avoid sticky molds is to ensure that you apply your release agent correctly.
There are different types of release agents available, such as petroleum jelly, silicone spray, and even cooking spray. However, not all release agents work for every mold material.
Silicone molds require silicone-based sprays while polyurethane and latex molds need a universal release agent like Ease Release 200. Another factor that can contribute to sticky molds is the number of layers applied on top of each other without proper drying time between them.
Inadequate drying time can cause layers to bind together and stick when removed from the finished product. If you find yourself with a sticky mold, it’s important not to panic or try to remove the piece from the mold forcefully as this will damage both the finished piece and the mold itself beyond repair.
Improper Curing: How Time Can Affect Your Finished Product
Another common issue that arises during resin casting is improper curing. Improper curing results in a soft or tacky finish that isn’t suitable for cosplay purposes or display purposes.
Curing times vary depending on different factors like temperature and humidity so it’s important not to rush this process. To avoid this issue, make sure you follow manufacturer instructions on mixing ratio and cure times carefully so you’re able to get an accurate result every time without relying too much on guesswork.
Another way you can ensure proper curing is by avoiding large batches when starting out with resin casting. This way, you’ll learn how long it takes to cure in a smaller quantity before moving on to larger batches.
If your cast appears tacky or soft, you may need to give it more time to fully cure. You can do this by putting your cast in a warm dry area for an extended period or using a heat gun at low temperature.
Sanding and Finishing: Getting the Smoothest Surface Possible
Another issue that can come up is difficulty with sanding and finishing. It’s important to remember that resin casting isn’t perfect and may not be as smooth as other materials like plastic.
However, there are simple solutions that can make your finished product look near-perfect. The first step is using proper sandpaper such as 400-600 grit before moving on to finer grits like 1000-2000 grit for a smoother finish.
If you’re struggling with uneven surfaces, try sanding with circular motions rather than back-and-forth movements. After sanding, give your finished piece some extra buffing with polishing cloth or compound followed by some wax for extra shine.
Air Bubbles: Eliminating Unsightly Imperfections
Air bubbles are another common issue that can arise during resin casting. They’re caused by improper pouring techniques and the only way to truly eliminate them is through correct mixing ratios and pouring technique.
To avoid air bubbles, make sure you mix thoroughly but gently so as not create too many air pockets in the mixture before pouring it into your mold. While pouring into your mold from a height or distance might seem like an efficient way of filling molds fast, it actually creates more bubbles over time due to the initial impact of the mix hitting the surface of the mold.
Instead pour slowly from one corner while tapping on the sides to help release any trapped air pockets trapped inside along the way tilting gently if necessary.. If you still have air bubbles, try using a toothpick/ pointed stick to gently push them out of the mix or use a heat gun to pop them out.
Uneven Mixture: Getting the Right Mixture for the Right Product
An uneven mixture can cause issues like an unoptimized consistency or poor curing time. One of the best ways to avoid this issue is to follow manufacturer instructions carefully and be mindful of mixing ratios when preparing your resin casting materials.
If you’re working with different materials such as powders, glitter, etc., make sure you add them in slowly while mixing. This will help ensure that they’re distributed evenly throughout the mixture without creating any lumps or uneven textures.
It’s also important to consider temperature and humidity when mixing your resin casting materials. These factors can affect curing times and can lead to an uneven finish if not taken into account properly.
Conclusion
Resin casting is a valuable technique to add to your cosplay skill set. It allows for incredible detail and accuracy, resulting in high-quality finished pieces that are sure to impress. As discussed in this article, resin casting offers several benefits over other methods such as foam or 3D printing.
It allows for the creation of lightweight, durable pieces that can withstand wear and tear over time. Additionally, it can be a cost-effective option for those looking to create multiple copies of a piece. These are some of our favorite cosplay on our instagram page.
While resin casting does require some initial investment in materials and equipment, it is a worthwhile investment for any serious cosplayer looking to take their craft to the next level. Plus, once you have the equipment and materials on hand, you’ll be able to create multiple pieces with ease!
It’s important to note that resin casting does require some practice and patience – don’t be discouraged if your first attempts don’t turn out perfectly! The more you practice, the better you’ll get at achieving an even pour and avoiding bubbles.
Overall, we highly recommend giving resin casting a try if you’re interested in creating high-quality cosplay props and accessories. With dedication and effort, you’ll be amazed at what you can create!